Products
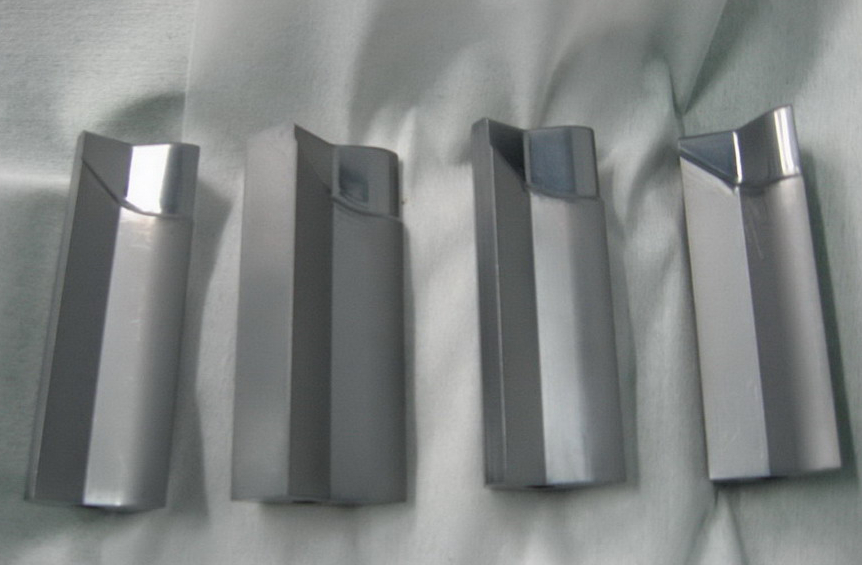


Nitriding | |
Nitriding treatment: refers to a certain temperature at a certain media manipulation nitrogen atoms into chemical heat treatment process workpiece surface. After nitriding treatment products with excellent wear resistance, fatigue resistance, corrosion resistance and high temperature properties. Order Hotline:400-6388-689 |
Nitriding treatment: refers to a certain temperature at a certain media manipulation nitrogen atoms into chemical heat treatment process workpiece surface . After nitriding treatment products with excellent wear resistance , fatigue resistance , corrosion resistance and high temperature properties .
Role:
Increased wear resistance, surface hardness, and resistance to corrosion fatigue limit of steel parts .
Technical process:
Parts of the surface cleaning before nitriding
Most part, you can use the gas to oil to the oil law immediately after nitriding . Some parts also need to use gasoline to clean better, but in the final process before nitriding method , if the use of polishing, grinding , polishing , etc., that may have hindered nitrided surface layer , resulting in post- nitriding, the nitride layer is uneven or bending and other defects. At this point should adopt one of the following two methods to remove the surface layer . Before the first method in the first nitriding gas to the oil . Then use the alumina powder to the surface for abrasive cleaning. The second method is about to be phosphate coating surface treatment (phosphate coating).
Nitriding furnace air exclusion
The parts to be treated is placed in the nitriding furnace , and heat sealed to the lid , it must be heated to 150 ℃ previous work for removing air furnace .
The main function is to exclude the furnace to prevent contact with air when ammonia decomposition occurs explosive gas , and be treated to prevent surface oxidation and stents. Gas they use ammonia and nitrogen that is two .
Exclude air furnace essentials as follows :
① parts to be treated properly installed sealed lid will begin through anhydrous ammonia, which may be more traffic as much as possible .
② automatically control the temperature of the furnace is set and started at 150 ℃ heated ( furnace temperature not higher than the note 150 ℃).
③ when the air vent in the furnace to below 10% , or the exhaust gas containing more than 90% of NH3, then the furnace temperature was raised to nitriding .
Ammonia decomposition rate
Nitriding is paved , and other alloying elements in contact with the nascent nitrogen carried out , but the generation of nascent nitrogen , ammonia and that is due to the heating of the steel material in contact when the steel material itself becomes a catalyst to promote decomposition of ammonia .
Although the variety of the decomposition rate of ammonia gas , can be nitrided , but generally 15 to 30% are used in the decomposition rate , to maintain a desired thickness and then nitrided at least 4 to 10 hours and the temperature is maintained at about 520 ℃.
Cooling:
Most of all industrial nitriding furnace with heat exchangers, to be rapidly cooled after nitriding furnace work is completed and the parts to be treated . That is, after the completion of nitriding , the heating power is turned off , reducing the furnace temperature about 50 ℃, and then the flow of ammonia increased to double the heat start switch being opened . At this point shall observe the exhaust pipe connected to a glass bottle , bubbles overflow whether to confirm the positive pressure of the furnace . Wait import furnace ammonia stability can reduce the flow of ammonia to keep the furnace positive so far. When the furnace temperature dropped to below 150 ℃, that the use of the foregoing exclusions furnace gas law , after the introduction of air or nitrogen before being opened lid .
Gas nitriding
Gas nitriding Department published in 1923 by the German AF ry, the workpiece is placed in the furnace , Lee NH3 gas nitriding furnace direct input of 500 ~ 550 ℃ , for 20 to 100 hours , so NH3 gas is decomposed into atomic state (N) of the gas (H) and gas nitriding treatment, the surface of the steel resistant, corrosion -resistant layer of a compound as the main purpose , of a thickness of about 0.02 ~ 0.02m / m, extremely hard nature Hv 1000 to 1200 , and very brittle, NH3 decomposition rate of flow size depending on the level varies with the temperature change , the greater the degree of decomposition , the lower flow rate , flow rate , the higher the smaller the decomposition , the decomposition rate , the higher the temperature , the higher , the lower the temperature the decomposition rate is also lower , NH3 gas at 570 ℃ when thermally decomposed as follows :
NH3 → [N ] Fe + 3/2 H2
The decomposed in N, with the diffusion into the surface of the steel is formed . Fe2 phase - 3N gas nitriding , hardening of the general shortcomings of thin and nitriding long time .
By the decomposition of NH3 gas nitriding low nitriding efficiency , it is generally applicable to both fixed selection nitrided steel , such as those containing Al, Cr, Mo and other elements of the nitride , the nitride few can not be otherwise , the general use of JIS, SACM1 new JIS, SACM645 and SKD61 to toughening treatment , also known as tempered by Al, Cr, Mo , etc. are to improve elements of the transformation point temperature , the quenching temperature is high, compared with ordinary structural alloy steel tempering temperature is high, which nitriding temperature between prolonged heating , tempering brittleness , so pre impose quenched toughening treatment . NH3 gas nitriding , surface roughness because time is long , hard and brittle and difficult to grind , and a long time is not economic for plastic injection feed tube and helical rod -shaped nitride machine .
Liquid nitrogen
The main difference is the soft liquid nitrogen in the nitride layer has Fe3Nε phase , Fe4Nr phase with the presence of free Fe2Nξ nitride , ξ phase compounds in the nitriding process is hard and brittle ductile bad nitride liquid tufftride the workpiece is to be processed , the first descaling, degreasing , and then placed in a preheated crucible nitride , the crucible is TF - 1 mainly of salts , are heated to 560 ~ 600 ℃ processed to a number of hours , depending on the size of the work load of the external force , but decided nitride layer depth , in the process , it must pass into the bottom of the crucible in an air duct to the air a certain amount of salt nitriding agent is decomposed into CN or CNO, penetration and diffusion to work surface, so that the outermost surface compound 8 ~ 9% wt and a small amount of C and N diffusion layer diffuses into the nitrogen atom α - Fe base manipulation greater fatigue resistance of steel due to the consumption during the decomposition of nitrogen CNO , so continue to test ingredients of salts in 6 to 8 hours of treatment in order to adjust the amount of air or adding new salt agent.
Soft nitriding treatment liquid iron metal material , the surface hardness after nitriding containing Al, Cr, Mo, Ti element by high hardness , the more gold and its nitride and more shallow depth , such as carbon steel Hv 350 650 stainless Hv 1000 ~ 1200, nitrided steel Hv 800 ~ 1100.
Soft liquid nitrogen for wear and fatigue resistance and other auto parts , sewing machines , cameras, etc. , such as cylinder liner treatment, gas treatment patriarch , dies at the piston cylinder handling and easily deformed . Soft using liquid nitrogen countries , Western European countries , the United States , Russia and Japan.
Ion nitriding
This method will be placed on a workpiece nitriding furnace , previously pumped into the furnace import N2 gas or gas mixture N2 + H2 of the vacuum of 10-2 ~ 10-3 Torr ( mm Hg) , the adjustment of the furnace 1 ~ 10 Torr, the furnace connected to the anode and the cathode connected to the workpiece , pass between the poles of a DC voltage of several hundred volts , then the N2 gas furnace discharge occurs glorious positive ions move to the work surface , the cathode in an instant voltage sharp decline , the positive ions at high speed toward the cathode surface , the gas can be converted into kinetic energy , making the surface temperature to rise , due to the impact of the workpiece surface after nitrogen ions play Fe.CO splash out in conjunction with other elements nitrogen ions into FeN, iron nitride, whereby the workpiece is gradually adsorbed generated nitridation , ion nitridation using nitrogen is substantially , but if the hydrocarbon -based gas may be added for a soft nitriding plasma , nitrogen plasma , but generally referred to treatment , the surface nitrogen concentration in the mixed gas in the furnace can be changed filled (N2 + H2) ratio of the partial pressure of a regulator , the pure ionic nitriding time in a single working surface r phase '(Fe4N) the amount of N -containing tissue in the 5.7 ~ 6.1% wt, thick layers within 10μn, this compound layer porous layer rather than tough , not falling , as iron nitride constantly being absorbed and spread to the interior of the workpiece from the surface to the interior of the organization is FeN changes → Fe2N → Fe3N → Fe4N order, single-phase ε (Fe3N) N content in the 5.7 ~ 11.0% wt, single phase ξ (Fe2N) N content at 11.0 ~ 11.35% wt, ion nitriding phase and then add the first generation r it becomes ε compound layer and the diffusion layer of the hydrocarbon gas phase system , the increase of the diffusion layer increases the fatigue strength has many help . The best corrosion resistance to ε phase .
Of the ion nitriding treatment can be started from 350 ℃, taking into consideration the material selection and processing time can be related to the mechanical properties of a few minutes so that the processing time , and the law in the past by thermal decomposition of the nitride reaction side processing different methods , Law Department of the use of high ion energy , in the past that refractory stainless steel , titanium, cobalt and other materials can also be simply subjected to a surface hardening treatment excellent .
Su's heat treatment Co. Ltd. was founded in 1990, after decades of development, scale is continually expanding, is located in Shajing Town Baoan District Shenzhen City Bridge second industrial zone, covering an area of 3000 square meters, the main business is to take all the metal, alloy steel, beryllium copper, heat treatment of high speed steel, cryogenic treatment (-196 C), nitrogen gas, liquid nitrogen, QPQ salt bath production line, high-frequency quenching, blackening and carburizing, the surface of hard and stainless steel processing.
The company is equipped with power of heat treatment technology, established a perfect quality testing equipment, equipped with vacuum quenching furnace, vacuum furnace, pit furnace, furnace, liquid nitrogen atmosphere furnace, rotary furnace, large mesh belt furnace, improve metallographic inspection equipment, material failure analysis, scientific management and complete, rigorous technology, skilled operation.
Company will be excellent quality and perfect service, and actively challenge, satisfy customer demand, has passed ISO9001:2000 in 2003 September (SGS) international quality certification. Has now become a reputable manufacturers.
Su's heat treatment (Shenzhen) Co., Ltd. Guangdong ICP No. 14020634
service hotline: 0755-27291255
Fax: support for 0755-27293730
E-MAIL:sushirechuli@163.com
Company address: Shenzhen, Baisha bridge Second Industrial Zone No. 14